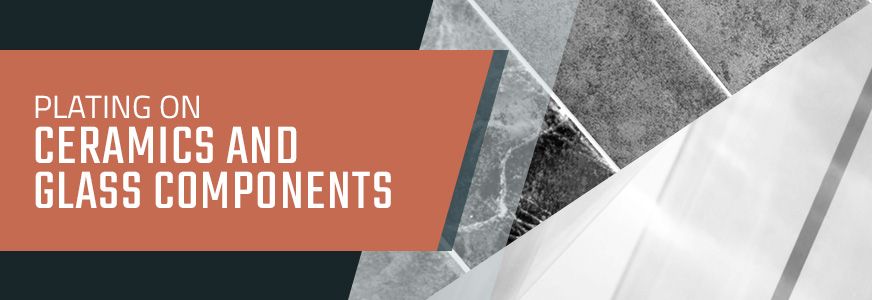
Quick Links
Plating on Ceramics and Glass Components | Methods of Plating on Glass and Ceramics
Electroplating Ceramic Surfaces and Glass Process | Electroless Plating of Ceramic and Glass Parts
Common Types of Metals and Alloys Used in Plating Ceramics and Glass | What Are the Advantages of Plating Onto Ceramics?
Ceramics & Glass Plating Services with SPC | Request a Quote
Plating on Ceramics and Glass Components
Plating on ceramic, glass and other materials like plastic is a proven method of instilling these otherwise fragile components with the desirable physical and mechanical properties of another material, specifically metals. While all components have different purposes and functions, they all need to perform under stress. Varieties of metals are used to provide manufactured components with the strength, longevity as well as thermal and electrical properties of a metal.
Like plastics, ceramics and glass are harder to work with than traditional materials, but these exotic materials offer beneficial thermal advantages, making them a commonly plated substrate for electronic components. Ceramics can withstand high temperatures, and when plated with a specific metal or alloy, gain strength and vital electrical conductivity for their use in electronic applications.
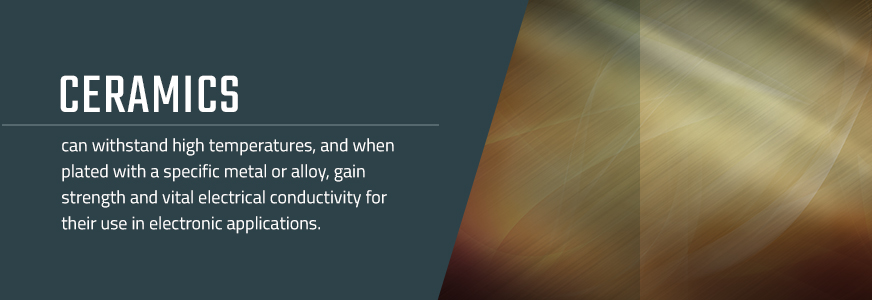
Commonly used metals and alloys in plating include copper, aluminum, tin, gold, zinc, silver and nickel. Metals offer both beauty and durability not found in the base properties of ceramics and glass. By adding metal to a ceramic or glass surface, you can provide a component with the essential mechanical, chemical and physical properties needed to ensure top of the line performance.
Whether you are trying to reduce corrosion or friction, or increase the strength, durability and conductivity of your component, plating it with a specific metal could be the solution. Whatever the case may be, selecting a component for plating is important.
Methods of Plating on Glass and Ceramics
Electroplating and electroless plating require different methods of completion. Electroplating necessitates the use of an electric current to adhere a thin layer of metal to the ceramic or glass substrate, while electroless plating relies on an autocatalytic chemical reaction for the same results. For electroplating, an electric current reduces dissolved metal cations, or ions with a positive charge. This procedure allows the cations to form a thin metal coating on the object through a process called electrodeposition.
Thinking about creating a circuit is a good way to understand the mechanics of electroplating. Electrodes adhere to a thin metal layer to the component. The component acts as a cathode, or negatively charged electrode, and the metal used is what makes up the anode, or positively charged electrode. At Sharretts Plating Company, we offer the highest quality in plating and finishing services and have mastered the demands of working with exotic materials such as plastics, ceramics and glass.
As these components are immersed in a bath of electrolytes comprised of metal salts and ions, this allows for the proper flow of electricity through the external electric current. This is supplied in the form of a direct current to the anode to help oxidize the metal atoms and dissolve them into the electrolyte solution. These dissolved metal ions in the solution reduce and begin to plate the object. The metal used for the anode continuously replenishes the ions in the electrolyte.
The electroless immersion processes do not require this type of external power supply and rely on an autocatalytic chemical reaction instead to perform its deposition. Electroless plating usually involves creating several reactions at once by immersing the component into a liquid solution. By using chemical methods, it forces the desired metal of choice to plate the object. Unlike electroplating, which requires two electrodes, electroless only uses one and is not dependent on any external electric current to perform the procedure.
Instead, reducing agents are used. For smaller components, this can be a cost advantage as electrolyte baths and the use of external power will increase overall expenditures. In addition, electroless methods of plating can offer flexibility in both the size and shape of components set for plating. The downside is that it can be much slower and will not be able to achieve the thickness that electroplating methods can.
Whichever plating method is most appropriate and cost effective for your component, the results are coatings of metal on a ceramic or glass substrate offering the tensile strength, hardness, durability as well as thermal and electrical properties of a metal.
Electroplating Ceramic Surfaces and Glass Process
When it comes to electroplating ceramic materials, adding a metal finish is a challenge. In most cases, this process will require an electroless nickel coating initially to promote adhesion of an additional metal finish. Almost any metal can be used with a ceramic substrate, and electroplating can be useful for this process. Once the ceramic component has received a thin metallic coating, it can be plated in the electrolyte tank process as with any other object.
On the surface ceramic seems fragile, but once the plating process has been finished, the product is durable. A number of different metals can be plated on ceramic, including precious metals like gold and silver. Depending on the metal selected, ceramic components can offer electrically conductive properties, reduce corrosion and inherit the resistance to wear.
Ceramic substrates are commonly used in the production of electronic circuits because they exhibit excellent thermal properties and performance. By plating them with a metal, it can increase conductivity and offer better physical and mechanical properties. In electronics manufacturing, aluminum oxide, silicon nitride and aluminum nitride are regularly used.
Low temperature co-fired ceramic substrates have also increased in popularity over the past decade because they offer enhanced performance through a mixture of material in layers. By using alumina and glass, these types of substrates can be co-fired with low-resistance metals like copper and silver at temperatures less than 1800 degrees Fahrenheit.
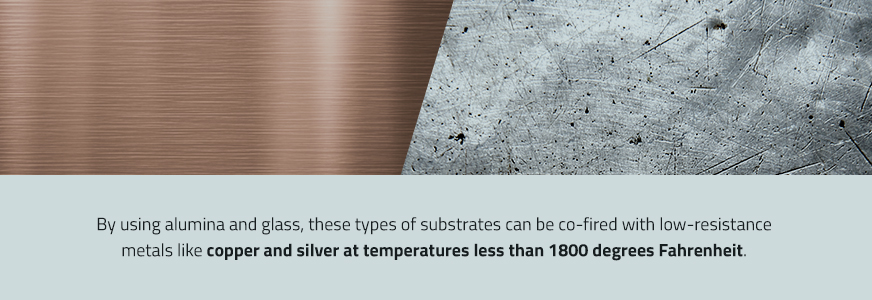
Electroplating glass parts offers its own unique challenges, as glass substrates often need to be prepared for the plating process. Copper and silver are some of the most commonly used metals for plating glass. These metals are popular because of their mechanical and physical properties, and are applied as a thin layer onto the glass surface of the component.
In order to prepare the glass for plating, conductive treatments are applied to the areas of the component where electroplating will occur. Graphite and other metal powders are used for the initial treatment of the substrate. One achieved, the component can then be submersed in the solutions of dissolved metals.
As with other electroplating methods, an external direct electric current runs from the anode — or metal used for plating — through the electrolyte solution to the negative electrode — or component surface — which has been treated to be conductive. In the final steps, changing the voltage provides the desired characteristics and determines the overall length of the electroplating process.
Request a free quote
For Ceramics & Glass Plating
Electroless Plating of Ceramic and Glass Parts
As mentioned above, electroless plating methods do not require the use of an external power supply to achieve a thin metal coating over a component's surface. However, the reliance on an autocatalytic chemical reaction still achieves similar results. In addition, electroless processes can be used for the preparation of ceramics, as the surface needs a thin layer to work for adhesion during electroplating.
Electroless methods are often reserved for smaller and different sized parts. The lack of external power and need for electrolyte solutions reduces overall costs.
Electroless deposition uses chemical solutions and a reducing agent to supply the electrons for metal deposition at a catalytic surface. Chemicals such as formaldehyde are used for electroless copper plating, while sodium hypophosphite is commonly used for electroless nickel plating.
As with electroplating, nearly any metal can be used for the finished product. Some of the most common for electroless plating include nickel, as well as a wide range of nickel alloys. Even if nickel is not the desired metal, professionals often use it as an initial layer so that other materials can be added to the ceramic component's surface.
Nickel, however, is not catalytic as an initial layer — and a catalyst must be deposited in order to facilitate electroless deposition. Once this process begins, nickel will build upon itself at a controlled rate.
When working with glass requires preparations before the electroless plating can begin. Copper and silver are among the metals most commonly used for deposition on glass substrates, but depending on the metal chosen, a thin coating of another material may be needed.
For example, for copper deposition on glass materials, it is common to use polyethylenimine (PEI) on glass matrix and epichlorohydrin (ECH) as a cross-linking agent to initiate the chemical reaction. Amino groups can effectively absorb palladium — the catalysts that initiate the copper electroless plating process onto the glass substrate surface. Copper film can then be formed on the palladium-activated glass surface.
Common Types of Metals and Alloys Used in Plating Ceramics and Glass
Ceramics and glass both provide challenges in the plating process, but nearly any metal can be used. Some of the most common include copper, nickel, silver and gold. Copper and its alloys are some of the most common types of metals used in plating because of their affordability and high electrical conductivity. Because of its high plating efficiency and its low cost, copper is one of the least expensive metals used, primarily in the manufacturing of electronic components and circuit boards.
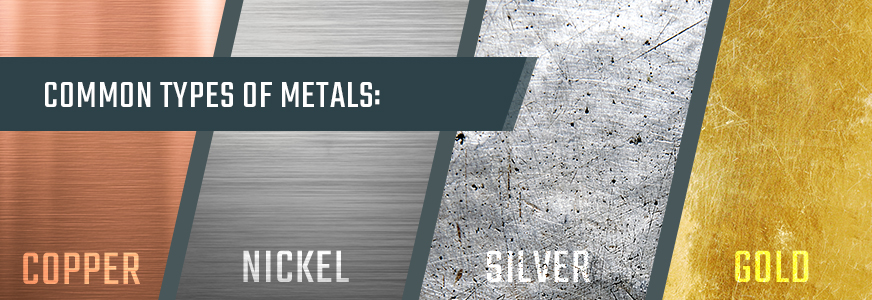
As mentioned above, electroless nickel plating is very common in both preparation and for finished products. Nickel and its many alloys are resistant to wear, making them widely used in the plating service industry. Nickel provides the basis that other metals adhere to during electroplating.
When it comes to precious metals, gold and silver both offer advantages of physical and mechanical properties. Gold offers a high resistance to oxidation, as well as high electrical conductivity. Unlike copper, gold is much rarer and more expensive. Because of its higher material cost, many reserve gold plating for small components. Gold is often used for electronic components — such as connectors — because it prevents rust and achieves the vital electrical conductivity in complex circuits.
Silver is another rare and expensive material, although not as expensive as gold. Silver is also used for electronics and offers enhanced electrical conductivity. Silver does not perform well in certain applications and has mechanical and physical properties that may not hold up in the long term compared to other less expensive metals and alloys.
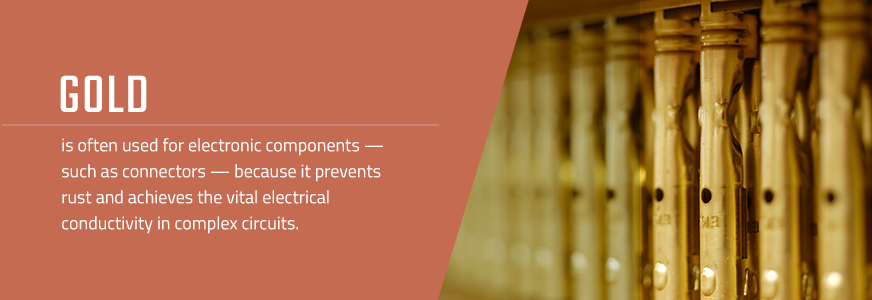
While traditional metals like tin, copper, nickel and zinc are all common in plating, certain exotic materials such as ceramics and plastics require superior metals to better withstand use over time. Stronger corrosion resistance and high electrical conductivity are often essential in these applications.
For nearly a century, Sharretts Plating Company has mastered the finished techniques of precious metals such as gold, silver, palladium and platinum, as well as a wide range of other precious metal alloys.
We can effectively plate other metals onto tungsten, as well as co-deposit tungsten with nickel and other standard metals. This has enabled us to make the transition from a traditional plating shop to a specialized, highly advanced metal finishing operation to meet the needs of industries such as medical, defense, aerospace and electronics. Working with exotic materials such as ceramics, glass and plastics, Sharretts Plating Company can provide you with results that will exceed your expectations.
What Are the Advantages of Plating Onto Ceramics?
The implementation of electroless plating and a variety of additional steps makes plating onto ceramics more challenging than traditional "metal on metal" finishing. However, the extra effort can offer several valuable benefits for your company:
- Making surfaces electrically conductive: Ceramic material is a poor conductor of electricity. Electroplating will "metalize" the surface to allow the product to carry an electric current, which is critical for manufacturers in the electronics industry.
- Improving appearance: Ceramics are not known for their brightness - an electroplated metal coating can add luster to an otherwise "dull" object, which can make it more attractive to potential customers.
- Enhancing strength and durability: Depending on their specific material type, ceramics exhibit varying degrees of hardness. A metal coating will make any ceramic product harder, enabling it to withstand the rigors of heavy use and increase the resistance to scratching, chipping, cracking and other forms of surface damage.
- Increasing corrosion resistance: While most ceramic materials are naturally resistant to corrosion, some ceramic-based products may be exposed to wet or moisture-laden environments. Metals such as gold and nickel will provide additional protection against rust formation, which can lengthen the product's lifespan.
- Giving you a competitive edge: The combination of these factors will result in a higher quality, better-looking ceramic product that customers will be more willing to purchase - and reorder when the time comes. In a time when obtaining and keeping customers is more challenging than ever, plating onto ceramics can have a positive impact on a manufacturer's revenues as well as what matters the most - the bottom line.
How Can Sharretts Plating Company Help Me?
Since 1925, SPC has been providing industrial plating services to a wide variety of industries, offering customized plating and metal finishing services to help our customers develop higher quality products and reduce operating costs.
Our industrial plating capabilities include everything from palladium plating to electroless nickel plating, copper electroplating to silver and gold plating. We also offer plating using various metal alloys that provide greater flexibility. Our plating business is one of the few in the industry that can effectively plate metals such as gold and nickel onto titanium, and we have perfected the difficult process of plating onto plastics.
We are one of the most environmentally friendly metal plating services operating today, and are constantly working to improve our metal plating and finishing processes to preserve the environment.
At Sharetts Plating Company, we can provide you with reliable and affordable services across a wide range of industries. If you’re interested in electroplating, electroless or other plating services, contact us today. We can provide you with a free quote for almost any industrial need. Our customer service representative will contact you within a single business day!
Additional Resources:
Contact Us TO LEARN MORE ABOUT OUR PLATING SERVICES
Contact SPC today to receive your no-obligation plating quote or to learn more about how our many valuable magnesium plating services can help you maximize your manufacturing processes.
LEARN WHAT OUR MANY SATISFIED CUSTOMERS HAVE TO SAY ABOUT Us
"I would like to thank you for the help you have provided us in developing an electroless nickel plating technique on an unusual substrate. The sample platings you provided show that we should be able to reach our goals. I especially appreciate your willingness to take on an unusual job, with the uncertainties that that entails...We are looking forward to working with you in the future on our plating needs."
– Robert K.