In addition, Electroless Nickel is used to coat titanium as an initial coating. These processing steps are conducive for effectively achieving a good bond to the titanium. Metals such as copper and gold are not used as first layers for metalizing on top of titanium, however subsequent finishes after the nickel is applied may be coated onto the nickel (such as gold plating or silver plating). When plating onto titanium, the result offers nearly the same corrosion-resistance capabilities as platinum and can limit the harmful impact of substances such as hydrochloric acid, chlorine gas and many organic acids.
Quick Links
Uses for Plating Onto Titanium | The Need for Titanium Electroplating
Issues With Plating on Titanium | General Surface Preparation Tips When Plating on Titanium
SPC: The Leading Plating on Titanium Company in PA and Beyond | Titanium Plating Services with SPC
Uses for Plating Onto Titanium
Titanium is used frequently in the aerospace industry, as its light weight aids in the ongoing demand for increased speed. Titanium can be alloyed with aluminum and other metals in the manufacturing of aircraft, missiles and spacecraft. Typical titanium applications include use in the production of key components such as landing gear, hydraulic systems and even aircraft engines.
In addition, titanium is able to provide protection against the corrosive effects of seawater, making titanium ideal for use in desalination plants. The automotive industry also uses titanium alloys in the manufacturing of cars and motorcycles that are used for racing because of its combination of light weight and superior strength.
Request a free quote
For Titanium Plating
Current Titanium Applications
In the following half century, the use of titanium in industrial and manufacturing applications has continued to grow. Common titanium applications now include:-
- Aerospace— Titanium can be found in many different types of aircraft. Its light weight can enhance the aerodynamics of an aircraft and provide increased fuel efficiency. Other beneficial properties of titanium include excellent fatigue, crack and corrosion resistance, and the ability to withstand relatively high temperatures. In addition to airplanes, titanium is also used in the manufacturing of missiles and spacecraft.
- Marine — Because titanium is capable of withstanding the corrosive forces of the salt found in seawater, titanium if frequently used in many marine applications. One common example is the manufacturing of components used in underwater surveillance cameras and other devices.
- Jewelry— Because titanium is extremely durable, lightweight and corrosion-resistant, it’s frequently used in the manufacturing of designer jewelry and watch cases. Titanium can also be colored easily, making it popular for use in body piercing.
- Medical— Titanium’s combination of light weight and superior strength makes it the ideal choice for medical implants such as the ball and socket joints used in hip replacements. Titanium is also biocompatible, meaning it is non-toxic to the human body. Many surgical instruments are now made of titanium. Other common medical applications for titanium applications include the manufacturing of crutches and wheelchairs.
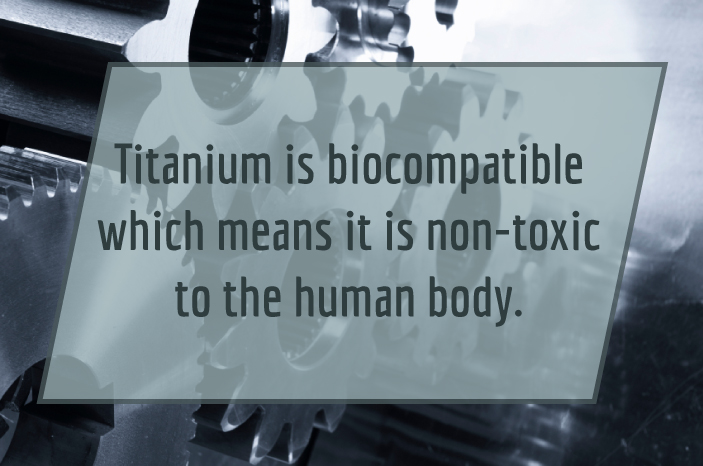
- Automotive— Titanium’s aerodynamic qualities make it suitable for use in the manufacturing of race cars.
The Need for Titanium Electroplating
While titanium on its own exhibits remarkable properties that make it amenable to manufacturing and industrial use, there are situations where plating on titanium and titanium alloys makes sense. In general, plating on titanium can help enhance the properties that already exist with the metal, making it even more beneficial to the manufacturing and metal finishing processes. Reasons to implement a titanium electroplating process include enhancing the metal’s ability to resist surface fatigue and fretting and anti-galling properties. Plating on titanium can also be used to improve corrosion resistance in extremely hot acidic environments, increase or decrease electrical conductivity, reflect heat, add lubricity, and repair and resize applications.
[contact-form-7 id="1010" title="Contact form 1"]Issues With Plating on Titanium
Plating on titanium has long been considered an extremely difficult, if not impossible, process to master. The biggest issue is that titanium is a highly reactive metal. Specifically, titanium reacts with the oxygen that is produced by many plating processes to form a passive film on the underlying substrate. This film generally prevents sufficient bonding of the metal coating that is applied during plating, rendering the process ineffective. In order for titanium electroplating to occur with any success, the chosen process must promote adhesion between the metal coating and the substrate. The method must also completely remove the native oxide and keep it away for the duration of the plating process. Finding a plating-on-titanium company that is capable of achieving each of these objectives can be nearly as difficult as the process itself. At present, there are only a handful of metal finishing entities that can provide a reliable cost-effective titanium electroplating process. Luckily, Sharretts Plating Company has the expertise and knowledge required to properly perform the titanium electroplating process.
General Surface Preparation Tips When Plating on Titanium
For starters, proper preparation of the titanium substrate surface is essential. There are a variety of methods that can be applied in the surface preparation process, including:- Conventional cleaning methods such as grinding, blasting, vapor degreasing and alkaline cleaning
- Activation via electrochemical etching without the implementation of heat treatment
- Activation by liquid abrasive blasting
Plating on Titanium With Nickel
Nickel is one metal that has been used for plating on titanium with a relatively high level of success. A nickel coating can increase the corrosion resistance of the titanium substrate and make it less susceptible to wear. In general, the process should consist of the following steps:- Use a solvent to degrease the substrate.
- Scrub the surface with a pumice powder paste in water.
- Apply an alkaline cleaner and rinse thoroughly.
- Immerse the substrate in a 500 ml hydrochloric acid/500 ml water solution and rinse thoroughly.
- Immerse the substrate in a hydrofluoric acid (48%) 120 ml/ nitric acid 400 ml/ Water to 1l solution and rinse thoroughly.
- Immerse in a hydrofluoric acid (70%) 130 ml/ Acetic acid 830 ml/ water 40 ml for anodic treatment.
- Apply a 15-30 ASF electrical current density at room temperature and rinse quickly.
- Immerse the substrate in a sulfamate nickel plating bath maintained at a temperature of 145°F and 1000 ASF and rinse thoroughly.
- Heat-treat in an inert-gas atmosphere at 480°C for two hours to promote adhesion.
Using Electroless Nickel Plating as an Undercoating
Electroless nickel plating is also sometimes used when plating on titanium. Unlike electroplating, electroless nickel plating does not involve the introduction of an electric current into the plating bath. Instead, an autocatalytic chemical reaction is used to deposit a nickel-phosphorous alloy onto the surface of the substrate. The electroless nickel plating process offers advantages such as a more uniform thickness and an even coating application.
When it comes to plating on titanium, an electroless nickel coating is normally not used as a finishing coat. Instead, it serves as a base coat for metals such as gold and copper for the purpose of promoting the adhesion of these metals to the underlying substrate. Other benefits of plating electroless nickel onto titanium include enhanced high-temperature oxidation and improved thermal conductivity, while also allowing for brazing and soldering.
Plating on Titanium With Gold
Gold is sometimes plated onto titanium as a means of enhancing the appearance of the substrate. However, because of the relatively high cost of this precious metal, only a thin layer of gold is normally applied to the titanium surface. An important factor in the success of any gold-on-titanium plating process is the total removal of titanium dioxide prior to plating to ensure a complete and continuous surface coating. One common issue when electroplating titanium onto gold is the formation of small holes, cracks and other surface imperfections. These problems can often be prevented by applying an electroless nickel coating prior to gold electroplating.
Electrodeposition isn’t the only method of plating gold onto titanium. A process known as chemical displacement is commonly used in the jewelry industry. A simple description of chemical displacement is the process of one element replacing another in a chemical compound. In the case of plating gold onto titanium, when the titanium is placed into a solution containing gold ions, the gold ions essentially replace titanium ions and are deposited onto the surface of the titanium object.
The bath used in chemical displacement consists of a precise combination of fluoride ions that dissolve the titanium oxide coating, monovalent gold ions, and citrate ions that serve the function of complexing the monovalent gold. Additionally, hydrogen ions are introduced into the batch to achieve the desired acidic state, and tungsten ions are used for batch preservation. The ideal concentration of each of these materials consists of:
- Monovalent gold: 25 grams per liter
- Citrate: 50 grams per liter
- Fluoride: 10 to 20 grams per liter
- Hydrogen: Appropriate amount to achieve a pH level from 5-6
When properly prepared and applied, this bath will produce a smooth, continuous gold plate that is free of surface defects. The gold plate is also known for its excellent adhesion to the substrate.
Plating on Titanium With Copper
Copper can be plated on titanium to improve electrical conductivity. As when plating gold onto titanium, it is advisable to first apply an electroless nickel coating. It’s also essential to remove titanium oxides from the surface. Here is a general overview of the process for plating on titanium with copper:
- Degrease with a solvent to remove contaminants and debris.
- Thoroughly clean the substrate with an alkaline solution.
- Rinse with deionized water.
- Blast with a water abrasive slurry.
- Rinse again with deionized water.
- Apply an electroless nickel coating to a desired thickness of 10 microns.
- Rinse with deionized water.
- Electroplate in an acid-based copper bath.
- Rinse with deionized water.
A final baking step is also recommended when plating copper onto titanium to promote adhesion. Heat treating should last for approximately one hour in a reducing atmosphere.