Plating for Medical Devices & Implants
The medical industry has made use of metal instruments for centuries, from the first scalpels and forceps to modern implants and scopes. As medical science has improved, the applications of metallic components have expanded and changed. Manufacturing techniques, in turn, have also advanced, increasing the design possibilities for metal components. Specifically, technological and medical advancements have made metal plating an essential part of modern medical device manufacturing.
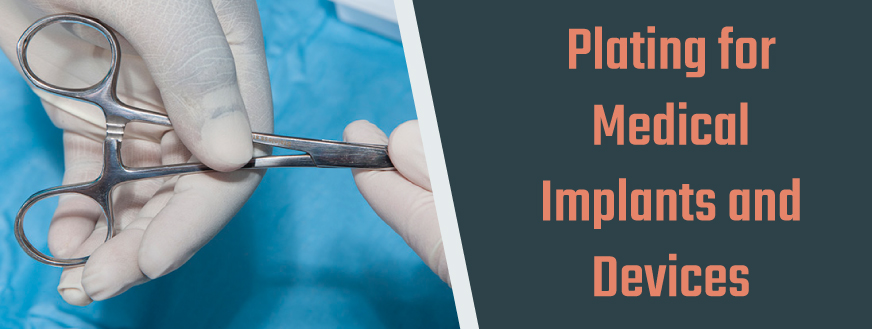
From surgical instruments to orthopedic implants, metal plating is commonplace in the medical device industry. While most devices are made with machined or pressed metal parts, many also use metallic coatings to improve the performance and quality of the final product. Metal finishes help ensure the safety of patients in both the short and long term especially for implants that are placed inside the human body, as the finishing process contributes to the compatibility of the implant with human tissue.
What is Medical Device Plating?
Typically, medical devices and implants are plated using an electroplating process, where a thin layer of precious metal is deposited onto a surface. Historically, this process was used in commercial and industrial manufacturing to improve corrosion resistance and electrical conductivity by depositing gold onto materials. With advancements in medical and manufacturing technology and increased collaboration between the fields, however, many more applications have come to the fore.
Electroplating is an additive process, including a series of steps to clean and activate a part before dipping it into a bath of dissolved metal atoms. The result is an exceedingly thin layer of metal, measuring down to 0.000003 inches. Though thin, this layer plays a significant role in the component.
Why Use Plating for Medical Implants and Devices?
The medical industry plates a wide variety of devices and implants, each for a different reason. Some of the benefits that can be gained by electroplating medical devices include:
- Sanitation: The medical field has strict cleanliness and sanitation standards that any medical product must meet. For reusable metallic devices, the surface that comes in contact with human tissue must be easily sanitized and discourage the growth of bacteria as much as possible. This helps keep bacterial infections to a minimum. To this end, most medical devices and tools are electroplated with materials that exhibit antimicrobial properties.
- Biocompatibility: Some types of metal will release ions or cause allergic reactions when implanted under human skin and kept in contact with tissue. Such metals will be plated with a biocompatible material to guard against such reactions so that the device will not cause problems when in contact with human tissue or internal organs.
- Electrical and Thermal Conductivity: Many modern medical devices operate using electricity, meaning that the efficient flow of electricity can make a difference in the device's functionality. For other devices that use heat, drawing heat away from the body can be a useful feature, minimizing the risk of burns. Various metals can be used for either of these purposes.
- Corrosion Resistance: Several types of medical equipment are repeatedly used and cleaned, including surgical clamps and scopes. Not only can repeated use promote corrosion and wear over time, but repeated cleaning with highly alkaline cleaning products can accelerate the onset of corrosion. Medical device coatings and electroplating can help slow corrosion and extend the lifespan of this equipment, reducing costs for medical organizations.
- Strength: Certain types of medical equipment require durable housing to withstand daily stresses and rough usage. Electroplating can serve either purpose, either by reinforcing a surface or by supporting a weld area to improve adhesion.
- Radiopacity: High-density metals like gold are radiopaque, meaning that they block radiation. By coating medical devices with such materials, one can create a radiopaque region that blocks radiation during X-ray procedures. This can help improve X-ray images.
These benefits can help both manufacturers and patients. While manufacturers benefit from the low material costs of electroplating devices, patients benefit from more sterile, more biocompatible equipment. Additionally, electroplating techniques help to keep devices relatively small, facilitating the development of instruments designed for minimally invasive medical procedures. Such procedures tend to be less expensive for patients, and require a shorter recovery time.
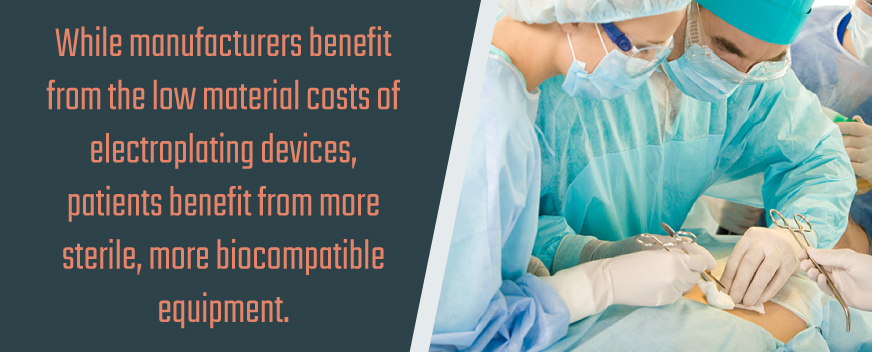
Common Plating Materials for Medical Applications
Medical metal finishing procedures use a wide range of metals, but here are some of the most common examples:
- Gold: Best known for its beauty and economic value, gold is a highly functional metal for medical applications. It features high biocompatibility and electrical conductivity as well as corrosion resistance. This makes gold a highly favored plating material for electrical connectors, heart stents, pacemakers and dental crowns, among other applications.
- Silver: Silver is another commonly recognized precious metal known for its beauty and value. Like gold, it is also highly useful for its electrical and thermal conductivity, as well as its antibacterial properties. These features make silver an ideal choice for many medical plating applications.
- Copper: Abundant and highly conductive, copper is suitable for electrical and thermal applications. It also happens to be highly resistant to bacteria, making it a frequent plating choice for medical devices.
- Tin: Affordable, non-toxic and corrosion-resistant, tin is another common plating material for the medical industry. It’s often used as a top coat for lead and tungsten shielding in radiological equipment.
- Nickel: This silvery white material is highly resistant to corrosion and is an excellent plating choice in many medical applications. Sulfamate nickel, with a high purity level, often serves as a ductile undercoat for gold and silver plating in electrical contacts. Nickel can also be plated using an electroless process, which retains the material's hardness while improving plating uniformity and corrosion resistance for medical devices.
- Platinum: This bright metal is hard and corrosion-resistant, as well as biocompatible, making it ideal for many medical applications. Some common medical plating applications for platinum include catheters, equipment connectors, pacemakers and implants.
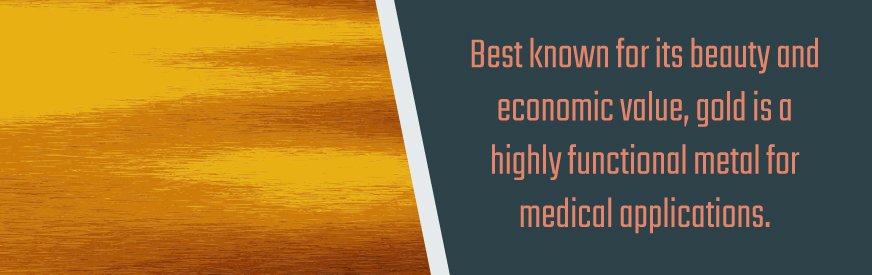
Each of these materials is used in a variety of medical applications. Manufacturers choose which metal to use based on the required functions of the device.
Request a free quote
For Medical Device & Implant Plating
Medical Applications for Plating
The benefits listed above have made metallic plating commonplace in the medical industry. A few examples of common applications include:
- Electrical Contacts: Gold plating is often used on electrical contacts for medical devices, both for its high conductivity and its resistance to corrosion.
- Catheter Braids: Electroplating is often used on the surface of medical catheter braids. This process functionally locks braid intersections together, improving the catheter's resistance to kinks. This not only improves insertion accuracy for medical professionals but also decreases discomfort to patients overall.
- Scope and Imaging Devices: Metallic components are included in arthroscopic and endoscopic tools, as well as scanning devices, which often need additional plating to protect against corrosion after long periods of use. High-density materials are also used in radiology to create radiopaque regions.
- Device Housings: Many tools like stethoscopes and radiological devices are housed in metallic structures to protect their delicate inner workings. Plating is often used to improve the durability of these housings in fast-paced medical environments.
- Implants: An implant is a device that is used to supplement or replace a biological structure. For example, orthopedic implants replace tissues that have been damaged due to trauma or a medical disorder, while cosmetic implants supplement existing structures for aesthetic purposes. Orthopedic implants replace joints like hips and knees and are often made of metal for the sake of durability. Plating for medical implants is highly desirable, as some types of metal are more biocompatible than others. Gold and titanium, in particular, are electroplated onto metal medical implants to improve biocompatibility.
Of particular interest in recent years is the latter of these applications, medical implants. Orthopedic implants are on the rise in the United States, with around 1 million joint replacement surgeries performed each year. With the prevalence of implants on the rise, improving implant quality through manufacturing and plating techniques is a high priority.
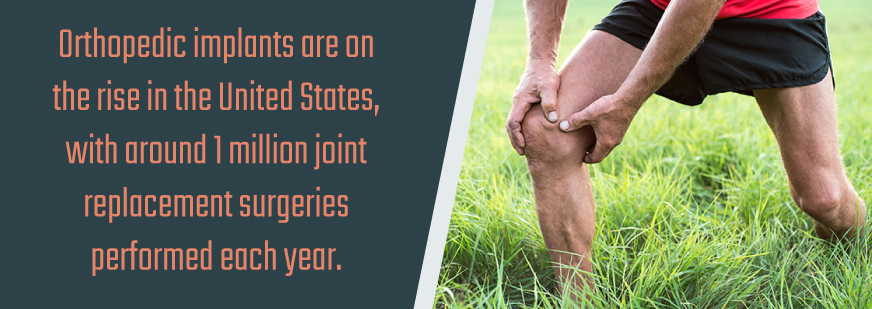
Common Base Materials for Medical Implant Plating
To understand medical electroplating for surgical implants more completely, one has to understand the materials commonly plated in these medical applications. The three most common materials are described in more detail here:
- Stainless Steel: Stainless steel is a metal alloy that has been used in surgical practices since the 1900s. Varying ratios of material result in different types of stainless steel, which are each best used for different purposes. For example, stainless steel type 302 was the first to be used in orthopedic surgery, but type 316L is now standard due to its corrosion resistance and purity. It's also non-magnetic, as magnetism interferes with MRI machines and promotes material heating, which can cause issues for the longevity of the implant and the comfort of the patient. Today, stainless steel is used in joint replacement prostheses, dental implants, stents and catheters, among other medical implants.
- Cobalt-Chromium Alloys: Cobalt-chromium alloys are nearly as popular as stainless steel, arising around the same time as stainless steel joint replacements. It was particularly favored for its corrosion resistance, and is also very strong, making it a popular choice for knee replacement prostheses. The biggest problem with this material, however, is the allergic reaction that it causes in some patients. Today, cobalt-chromium alloys are used to produce dental implants, orthopedic fracture plates, heart valves, spinal rods and joint replacement prostheses.
- Titanium: Though the material is relatively new in the field, many modern medical devices are made of titanium and titanium alloys rather than stainless steel. Some examples of common titanium implants include cranial plates, dental implants, orthopedic fracture plates, joint replacement prostheses, stents and catheters. Titanium is favored primarily for its strength to weight ratio – titanium retains the strength of stainless steel while weighing approximately half as much. While these qualities make titanium for surgical implants highly desirable, the material is much harder to work with than stainless steel, as it corrodes in the presence of hydrogen, nitrogen and oxygen. To combat the material's susceptibility to corrosion and improve its strength, titanium is often plated with nickel and platinum. This process is challenging, however, due to the reactive nature of the metal.
- Magnesium: Medical manufacturing researchers are currently exploring the use of magnesium in implant manufacturing. This lightweight material is strong, like titanium, and yet is biodegradable, which eliminates the need for additional surgical procedures to remove the implant once it has served its use. While this biodegradability is useful, it also makes magnesium difficult to coat.
- While these metals are used in the primary structure of an implant or device, they are often electroplated with a second material, lending them properties they would otherwise not have. Coatings are also often used to help these materials integrate more completely with bone and other biological tissues.
Medical Implant Coatings
Medical implants often require specialized manufacturing to work appropriately and integrate into the human body over an extended period. To this end, medical implants often employ coatings. Coatings are metallic additions to the surface of a medical implant, which are plated onto an implant to improve its functionality and prevent the release of ions into the body. Some common examples of coatings for medical implants include:
- Diamond-Like Carbon (DLC): This carbon-based coating is composed of diamond and graphite bonds, lending it diamond-like properties. Extremely hard and tough, DLC coatings are highly biocompatible but suffer from issues like chipping due to poor adhesion. Research is currently underway to improve DLC coating adhesion.
- Titanium Nitride (TiN): This material is a type of ceramic, commonly favored for its hardness and its ability to be added directly to a titanium or titanium alloy surface. This medical-grade titanium coating is often employed in joint implants, like hip or knee implants, due to its durability and biocompatibility.
- Graphite-Like Carbon (GLC): Recently found to have potential as coating, GLC may be able to extend hip joint life expectancy to over 50 years. The material possesses many positive mechanical properties like hardness and flexibility.
- Tantalum (Ta): This coating has excellent potential, as the material is hardy and flexible, as well as highly biocompatible. In fact, a recent scientific review determined that Tantalum-coated implants have the lowest average wear rate compared to the other coatings listed here, though further research will likely be required to fully explore the benefits of each coating type.
By using and improving upon these coatings, medical implant manufacturers hope to extend the lifespan of artificial joints from 15 years to half a century or more.
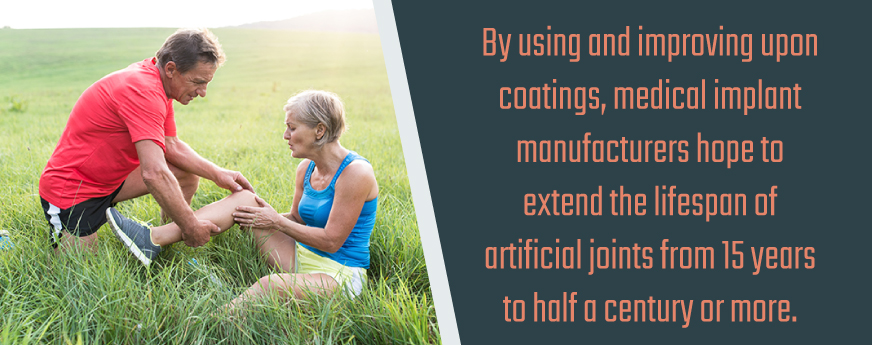
Challenges in Medical Implant and Device Manufacturing
Though medical device and implant manufacturing has made substantial headway over the past few decades, research continues to advance to improve the quality of implants and devices in the following areas:
- Wear: Wear over time is a major issue in implant manufacturing, resulting from the movement of an implant and exposure to human tissue. In joint replacements, this wear often occurs at the site of articulation, caused either by the friction at the articulation site or by the presence of foreign materials at the joint. Research continues to progress in this area to minimize wear over time through the use of electroplated materials and coatings.
- Cohesive Failure: The integration of a medical implant into the body is another major issue for medical implant manufacturing, one which is most concerning for joint replacements. For a joint replacement to work properly, the joint must integrate with the surrounding natural bone through a process called osseointegration. This process is often sped along through the use of screws and pitting in the surface of an implant, which encourages bone growth at the implant site. However, this joint can fail if the implant isn’t properly installed or if the patient’s bone growth doesn’t take. Excess stress at the joint can also result in cohesive failure. Any of these factors can cause the joint to fail, meaning that another joint replacement may be necessary.
- Biocompatibility: Biocompatibility is an issue concerning all medical implants and devices, as the surface of the implant will be in contact with the internal environment of the human body. While many metals are biocompatible, some people may be allergic to certain metals, requiring the use of an alternative material. Biocompatibility can also be enhanced with coatings.
These challenges make it imperative to choose a plating company with extensive experience in medical electroplating. That’s where Sharretts Plating Company can help.
Sharretts Plating Company Can Help with Your Medical Device Coatings
SPC has extensive experience in medical device and implant coatings of all types and sizes. Backed by over 90 years of metal finishing experience, you can depend on SPC to develop a process for your unique project. From gold and platinum electroplating to plating onto platinum, we can help your organization with your next plating project.
At SPC, we have the staff, facilities and technical resources to meet every one of your plating needs. ISO-certified and dedicated to constant improvement, SPC can guarantee your company the highest possible quality in medical finishing services.
Contact SPC today to learn more about us and our medical plating services and receive a free, no-obligation quote.
Additional Resources:
LEARN WHAT OUR MANY SATISFIED CUSTOMERS HAVE TO SAY ABOUT Us
"I would like to thank you for the help you have provided us in developing an electroless nickel plating technique on an unusual substrate. The sample platings you provided show that we should be able to reach our goals. I especially appreciate your willingness to take on an unusual job, with the uncertainties that that entails...We are looking forward to working with you in the future on our plating needs."
– Robert K.